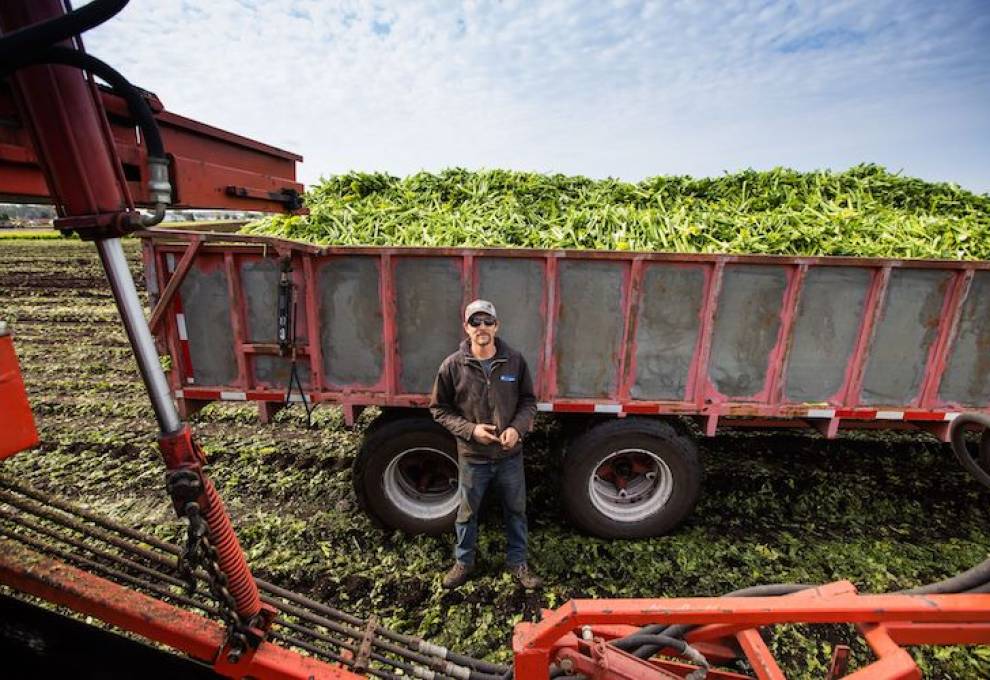
The lure of U.S. processing contracts is about more than the exchange rate – although, admittedly, it’s tipped in favour of Canadian exporters this year. For celery grower Tim Horlings, it’s about minimizing the time that he owns the crop.
“I don’t have to store it,” says Horlings, as he watches a tractor trailer rumble out of his Newmarket, Ontario farm drive. The load will be delivered in under eight hours to Hanover Foods Corporation.
Situated in Pennsylvania – about 700 miles south as the eagle flies – Hanover Foods Corporation is the largest fully-integrated and independent food processor in the United States. The maw of a plant transforms raw vegetables into canned, frozen, refrigerated and freeze-dried foods.
‘Supporting local farmers since 1924’ may be the tag line for Hanover Foods Corporation, but some of its daily bread depends on Canadian celery. As Horlings explains, American farmers don’t stack up the same celery yields as those growers in Ontario’s Holland Marsh.
“We produce a higher tonnage on smaller acreages,” says Horlings, whose father and uncle started the trek to Pennsylvania back in the early 1990s. Blessed by muck soils and access to irrigation water, the family has specialized in processing celery that forms the flavour base of soups, stews and chowders.
Since taking over the farm in 2006, Horlings starts every March by planting Norseco’s Sabrosa variety of celery in his greenhouses. By May, the seedlings are big enough to be transplanted. One might think that the agronomics of a processing variety would be less demanding than celery for the retail trade. Not so. To achieve volume yields, the crop must receive a weekly dose of micronutrients. Boron and calcium, in particular, are needed to form strong cellular walls to support the six-pound heads at 100 days of maturity. These are twice the size of celery bound for grocery stores.
“We take tissue samples every week so that we can adjust micronutrient needs and adapt to the weather,” says Horlings.
Protective fungicides are equally important to assure quality appearance of the celery.
By August, diseases such as bacterial leaf spot, celery leaf curl and blackheart may “take down” plants. Why so fussy if the celery is going to be chopped and diced into Chicken Pot Pie soup? The processor’s specifications require unblemished straight stalks of celery.
As Horlings explains, every grower wants stalks, not leaves. Upon arrival at the processing plant, the load is probed for percentage of leaves. Six per cent is the processor’s tolerance level to avoid penalties. His celery averages two to three per cent, but the goal requires all-season care. He also ensures quality with his own fabricated equipment that chops the celery into six-inch sticks whilst still in the field. Shredding celery leaves and leaving them on the soil to decompose is a better stewardship move than sending them stateside.
“I contract (with Hanover) at the start of the year on how much we’re going to grow,” says Horlings. “It’s simply less of a gamble to not have to store the crop. I consider this a cash crop.”
With 70 acres on contract in 2021, Horlings is smiling. The loonie’s tumble has been in his favour from a high of 0.83070 USD on June 2, 2021 to a low of 0.78409 USD on July 19, 2021.
Not every field vegetable grower is feeling as confident about future prospects. Mark Srokosz, a long-time grower of carrots and celery, notes that fewer vegetable acres were planted in the Grand Bend, Ontario vicinity this year. Industry observers confirm the loss of 500 acres of broccoli and 200 acres of onions province-wide. And that estimate may be low.
Srokosz says that celery contracts were cut by local processors due to less demand from foodservice. Costs of fertilizer and crop protection products continue to rise. Growers have worries about access to labour for critical harvest periods. The burdens of these new work-related concerns amidst COVID-19 lockdowns have taken a personal toll.
“The fresh vegetable business is in a state of emergency,” declares Srokosz. “The costs of production are driving Ontario growers out of business. This coming winter, there will be hard decisions to make.”
These contrasting stories illustrate the different paths that individual growers take to keep their operations sustainable and profitable. For them, this fall’s federal election is punctuating a difficult 18 months. The path forward will be influenced by policies in labour, housing, crop protection and value-added processing in a country that could be more self-sufficient in its food production.
Dr. Evan Fraser, director of the University of Guelph’s Arrell Food Institute, points out a need for a reset.
“Our current food system is based on assumptions of high productivity supported by access to water and an open border. That may not be the case for the next generation of farmers,” says Fraser.
He would like to see a renaissance of a local processing industry that can turn raw ingredients into value-added products. A more sustainable food system would include research into improved cultivars, combined with new technologies that can extend the growing season to year-round.
The greenhouse sector has proved, in spades, that innovative practices can produce tomatoes, peppers and cucumbers, and more recently, strawberries, on a year-round basis. Now the movement, from other growers, is towards high tunnels to extend the season for a variety of crops.
Fresh vegetable growers such as Tim Horlings and Mark Srokosz have limited options. It’s an open-ended question how the business of field vegetables will evolve in such a competitive landscape.
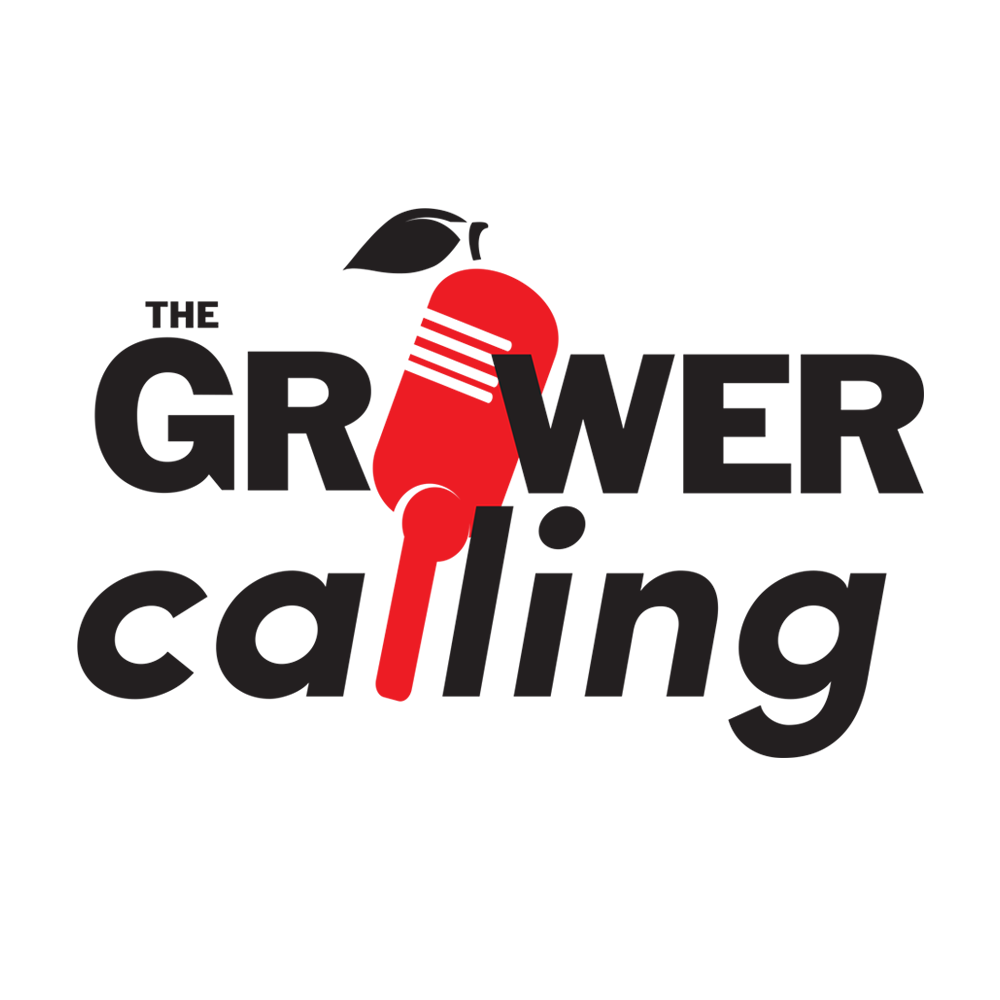